Log-in here if you’re already a subscriber
Air safety reporting by The Air Current is provided without a subscription as a public service. Please subscribe to gain full access to our all scoops, in-depth reporting and analyses.
An expert panel drawn from industry, government, labor and academia has published its Congressionally mandated report on the FAA’s Organization Designation Authorization (ODA) granted to Boeing. The Feb. 26 report (PDF) draws stark conclusions about the deep fractures and strategic disintegration within the company’s attempts to build a safety culture through numerous organizational changes, including the establishment of a formal safety management system (SMS).
The panel said it reviewed more than 4,000 pages of Boeing documents, conducted seven surveys and over 250 interviews that stretched from those on the factory floor to the company’s senior management, in addition to holding meetings with Boeing employees across six company locations.
“The depth of analysis that has gone into this report is unprecedented,” said Dr. Najmedin Meshkati, a professor of civil and environmental engineering at the University of Southern California, an expert in human factors research, and a member of the expert panel in an interview with The Air Current.
Related: Boeing’s MCAS on the 737 Max may not have been needed at all
Meshkati, who along with 23 other panelists crafted the 50-page report over the last 12 months, examined the influences within Boeing corporate culture on the company’s safety culture. The report is particularly damning, not only in its conclusions about the current state of Boeing’s safety culture, but also in its conclusion that directly ties several decades of the company’s corporate decision making to an erosion in aircraft safety.
While Boeing in its messaging since the 2019 and 2020 737 Max grounding has emphasized safety as its “highest priority”, critically, “the panel observed documentation, survey responses, and employee interviews that did not provide objective evidence of a foundational commitment to safety that matched Boeing’s descriptions of that objective.”
“The Expert Panel observed a disconnect between Boeing’s senior management and other members of the organization on safety culture,” it wrote.
Related: FlightBlogger – July 2009 – Commentary: It’s time for Boeing to talk. To itself.
The panel — made up of experts from NASA, FAA, Boeing, the Air Line Pilots Association, Allied Pilots Association, the leadership that represents Boeing’s unionized machinists, Gulfstream, GE Aerospace, Bell Textron, Pratt & Whitney, American Airlines, FedEx Express and United Airlines, among others — recommended that Boeing within six months develop an action plan that addresses the findings and the 53 separate recommendations to the company and the FAA.
“It is not only for Boeing,” said Meshkati. “The findings of this panel, as far as public policy, is applicable to every equipment manufacturer or operator…in safety critical industries,” he said, specifically referencing the healthcare, oil-and-gas and nuclear power industries as direct beneficiaries of the report’s findings and lessons. Meshkati was also involved in authoring a report from the National Academy of Engineering on the 2010 BP Deepwater Horizon accident and one from the National Academy of Sciences on the 2011 Fukushima Daiichi reactor meltdown.
Boeing said in a statement, “We transparently supported the panel’s review and appreciate their work. We’ve taken important steps to foster a safety culture that empowers and encourages all employees to share their voice. But there is more work to do. We will carefully review the panel’s assessment and learn from their findings, as we continue our comprehensive efforts to improve our safety and quality programs.”
Boeing’s internal reforms following the 737 Max crashes included the creation of a chief aerospace safety officer (CASO) and realignment of its engineers to report up to the Chief Engineer and a newly established Aerospace Safety Committee. The centerpiece of Boeing’s changes was the implementation of a comprehensive SMS, announced in September 2019 and formally accepted by the FAA for its commercial airplane unit the following year — though Boeing had already pledged to implement an SMS as part of an FAA settlement in 2015 around multiple production issues and resulting enforcement actions.
In assessing its performance in recent years, “Boeing did not produce quantifiable measures which led Expert Panel members to conclude Boeing is not actively monitoring the efficacy of these [safety] initiatives,” according to the report. The panel also noted that as part of Boeing’s safety culture improvement that underpins its SMS the company has sought to emphasize three safety “behaviors”: to “Seek, Speak & Listen”. However, the “Expert Panel observed throughout the discovery and assessment process that…little or no attention [was] given to Seek or Listen.”
“Boeing employees across all disciplines and roles expressed concerns over the lasting power of the SMS program and safety initiatives. This raises concerns about the sustainability of SMS. The lack of feedback and/or delay in providing feedback jeopardizes the longevity of SMS,” the report noted.
Related: New document in 737 Max investigation points to chaos, pressure in MCAS development
The panel gave Boeing credit for restructuring the management of the ODA Unit Members (UMs) — Boeing employees responsible for approving items on behalf of the FAA. The restructuring “decreased opportunities for interference and retaliation”, but “while better, still allows opportunities for retaliation to occur, particularly with regards to salary and furlough ranking. This influences the ability of UMs to execute their delegated functions effectively.”
The panel noted a key finding that interviewees shared examples of “unintended consequences when concerns of potential interference and retaliation are raised. Some UMs reported changes in behavior from their leadership and unrequested changes in assignments.”
Physical separation and geographical distribution also played a key role in perceived unevenness in the company’s ODA. “Specifically, non-Renton and non-Everett sites felt less supported by ODA management. The physical separation between the sites causes employees to feel communication is not at the same level as the main sites.”
Related: Boeing slows way down on Chinese 737 Max production
Crucially, the panel also said in its finding that it is “concerned that Boeing is not taking sufficient actions to maintain and expand its UM pipeline.” This not only puts the efficacy of delegated authority at risk with “efforts to retain them [that] are not effective or timely” but also, “given the timeframe required to properly train a UM, and taking sufficient actions to maintain and expand its UM pipeline will be key for Boeing to maintain or expand its current production rates.”
Flight deck design
The panel placed significant emphasis on human factors and their contribution to flight deck design. This was a key element in the 737 Max crashes, resulting from multiple, confusing warnings related to erroneous angle of attack data that concurrently triggered the Maneuvering Characteristics Augmentation System (MCAS) — the central cause in the loss of control of both Lion Air and Ethiopian Airlines flights in 2018 and 2019.
Related: Inside the convoluted politics of certifying the last 737 Max models
The panel noted systematic deterioration in Boeing’s human factors capability, pointing to the development of the 757 and 767 in the late 1970s and early 1980s — airplanes with common cockpits and type ratings despite different handling characteristics — as having been positively influenced by the expert teams within Boeing in Seattle. “At the time, [Boeing Commercial Airplane]’s human factors in flight deck design and operations were the gold standard with pilots, engineers, product support, and human factors specialists.”
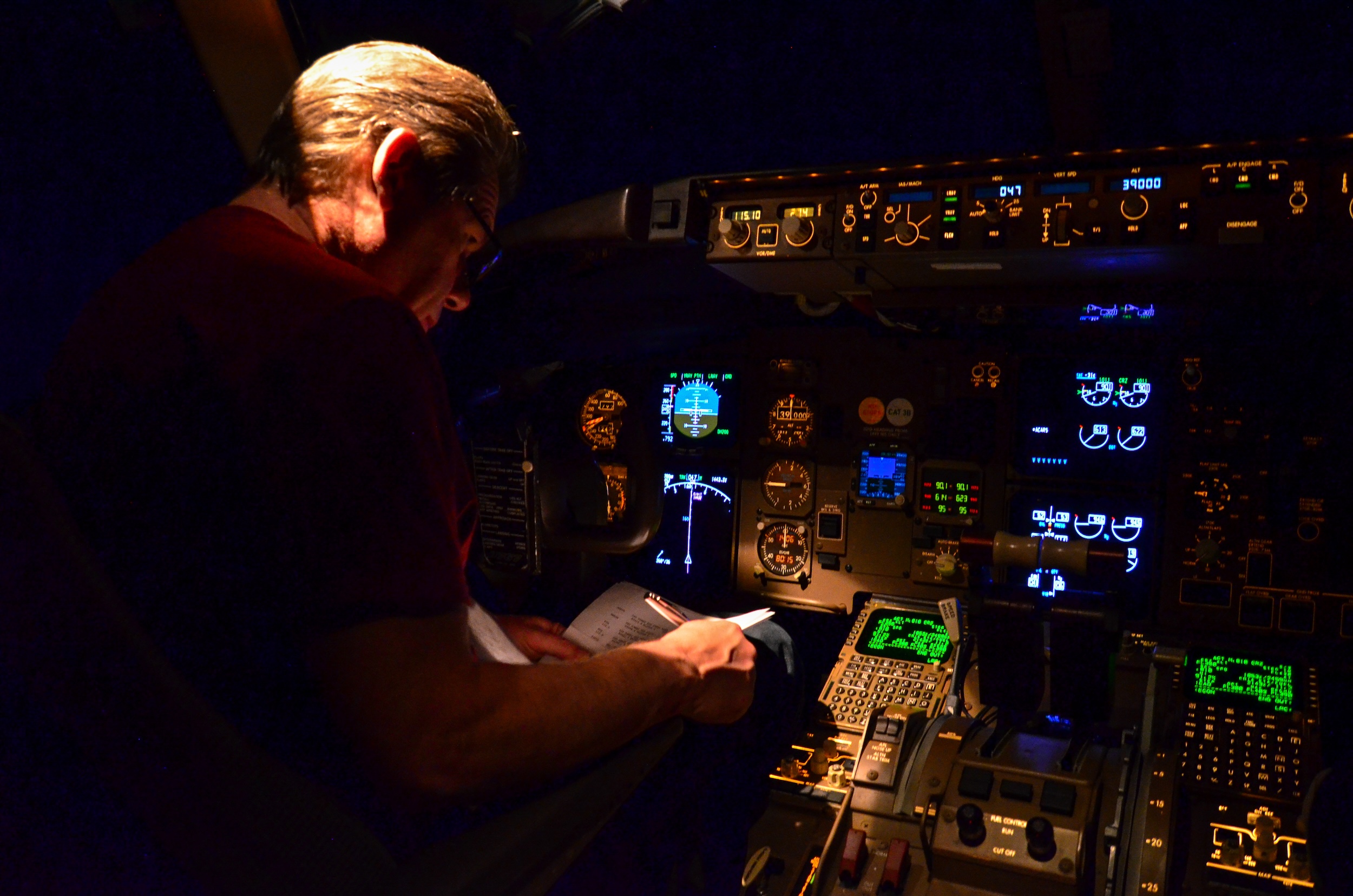
“Since then, the role of human factors and its influence eroded due to a series of administrative decisions at Boeing, which includes reorganization, decentralization, downsizing, and relocating the company’s headquarters,” the panel wrote, in one of the most sweeping conclusions established across official expert reports amassed over the last five years that have dissected Boeing and the fundamental causes of the Max crashes and the company’s struggles. (Unrelatedly, the Securities and Exchange Commission Monday formally blocked a shareholder proposal from a vote that would have urged relocation of Boeing’s headquarters back to Seattle.)
The report also concluded there was “inadequate human factors consideration commensurate to its importance to aviation safety and [a] lack of pilot input in aircraft design and operation.”
Related: Checklists come into focus as pace-setter for 737 Max return
“Boeing’s pilots are uniquely qualified to identify safety issues and hazards inherent to the aircraft design that may affect the safe operation of an aircraft,” the report found, also noting that interviewees believed pilot concerns were neither adequately communicated nor consistently delivered within the organizational structure if the pilot delivering the input did not hold an executive position.
The report said the company is “in the process of rebuilding its human factors capability” within commercial airplanes as a “stand-alone, and highly prioritized technical discipline and design practice within Boeing”.
The report defines a “design practice” as the “collection of engineering design requirements, instructions, guidance, and experience into a standard” and the assembly of subject matter experts “charged with enforcing the design standard, and reviewing and approving any deviations to the standard.”
Meshkati said the central conclusion “is not only about aviation” emphasizing the need for user-centric design, underpinned by a design practice, for safety critical products and systems.
The panel sought to solicit feedback and perspectives on its work, though it noted that some Boeing employees it spoke with viewed the panelists’ activities as “an audit; not an opportunity to collaborate.” The report noted, “Some interviewees mentioned a briefing was provided by Boeing legal prior to the interviews.”
Related: 127 Days: The anatomy of a Boeing quality failure
In its interviews, the panel found that ODA Unit Members, those who are tasked with being delegated representatives of the FAA, “questioned whether Boeing’s safety reporting systems would function in a way that ensures open communication and non-retaliation.”
The report was a key piece of the 2020 Aircraft Certification, Safety, and Accountability Act passed in December 2020 in the wake of the twin crashes and grounding of the 737 Max. The authors of the report noted that it was not directed to “investigate specific airplane incidents or accidents” as part of its work, though “serious quality issues with Boeing products became public” during this process, a reference to the Jan. 5 accident aboard Alaska Airlines 1282.
“These quality issues amplified the Expert Panel’s concerns that the safety-related messages or behaviors are not being implemented across the entire Boeing population.”
Write to Jon Ostrower at jon@theaircurrent.com
Subscribe to Continue Reading
Our award-winning aerospace reporting combines the highest standards of journalism with the level of technical detail and rigor expected by a sophisticated industry audience.
- Exclusive reporting and analysis on the strategy and technology of flying
- Full access to our archive of industry intelligence
- We respect your time; everything we publish earns your attention