Log-in here if you’re already a subscriber
Air safety reporting by The Air Current is provided without a subscription as a public service. Please subscribe to gain full access to all our scoops, in-depth reporting and analyses.
In the decade leading up to the 2023 fatal crash of a U.S. Air Force V-22 Osprey off the coast of Japan, there were 10 previously unreported in-flight V-22 component failures attributed to the same material defect that is suspected as the root cause in the crash. This persistent manufacturing problem was well known and analyzed by manufacturer Bell Boeing and the V-22 Joint Program Office, yet pilots were not given information about a systemic and ongoing risk to the Osprey fleet that could have changed how they responded to in-flight indications of possible failures, according to documents reviewed by The Air Current.
Non-public risk assessments by Bell engineers in addition to publicly available records associated with the investigation into the Air Force crash paint a picture of a thorny manufacturing problem in the background of a program that was already saddled with a negative safety reputation and a history of fatal accidents. It is not clear why details of the specific risks posed by this material defect were not shared with V-22 operators, but a better understanding of them could have potentially altered decision-making by the accident pilot, who has received much of the blame for the accident in the absence of publicly available information about the defect.
Air Force Special Operations Command (AFSOC) on Aug. 1 released its public report on the investigation into the crash concluding that the accident — or “mishap” in military parlance — was caused by a catastrophic failure of the CV-22B’s left-hand proprotor gearbox (PRGB) and the pilot’s decision to continue flying past other possible landing locations after being alerted to metallic chips in the gearbox oil. All eight people on board were killed when the aircraft crashed into the water near Yakushima Island, Japan, on Nov. 29, 2023.
The investigation determined that the gearbox failure was most likely initiated by cracking in a high-speed pinion gear and its associated bearing cage. Although investigators were unable to conclusively determine the cause of the cracking, they speculated that it may have been the result of an inclusion — a foreign substance within the raw steel material that creates a weak point.
Bell Boeing and Naval Air Systems Command (NAVAIR), which manages the V-22 program for the Air Force, Marine Corps and Navy, have known since 2011 of inclusions in the steel alloy, known as X-53, used to make the V-22’s power gears and outer clutch races. The first in-flight gear failure attributed to an inclusion occurred in 2013. All 10 of the previous in-flight failures produced metallic chips and cockpit alerts similar to those seen in the Air Force crash, and all landed safely.
Engineers at Bell, which is responsible for the V-22’s drive system, prepared multiple formal safety assessments of the risks posed by inclusions in X-53, including non-public reports from 2014, 2020 and 2022 that were reviewed by TAC. They concluded that depending on specific operations and analytical assumptions, the risks of an inclusion-related catastrophic failure resulting in death and/or loss of the aircraft ranged from “improbable” — highly unlikely — to “remote”, meaning it could be reasonably expected to occur during the life of the V-22 fleet.
In numerical terms, the definition of remote corresponded to a probability of at least one event per million flight hours (10-6), a likelihood far higher than the one event per billion flight hours (10-9) that is the standard in commercial aviation. The V-22 fleet has already flown more than 700,000 flight hours, and over their service life, military aircraft models typically log multiple millions of hours across the fleet. Two of the assessments characterized the risk to the program as “serious”.
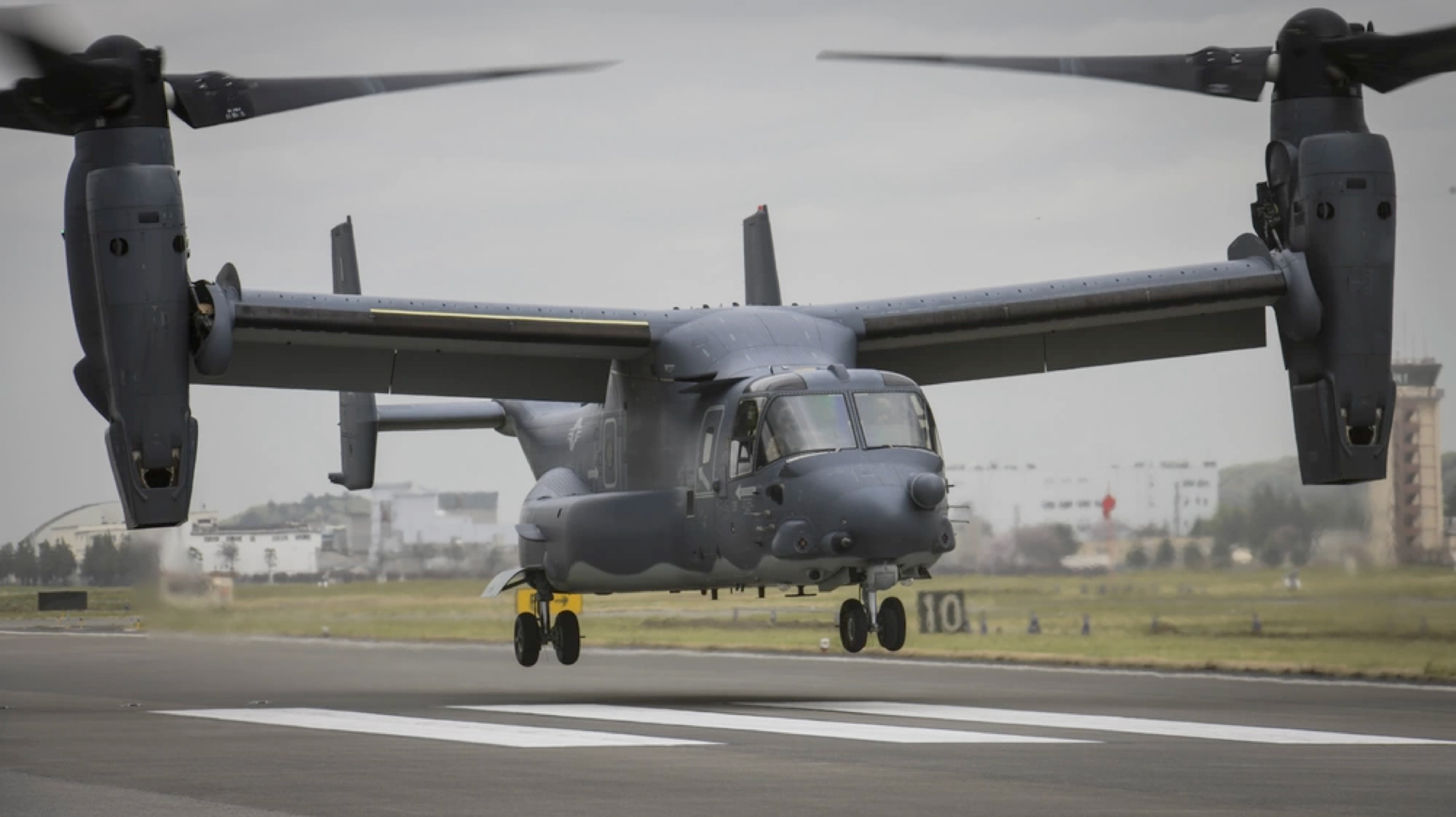
The safety assessments relied on assumptions that pilots would land promptly after receiving chip alerts — indications that a magnetic chip detector has attracted a small piece of metallic debris in the gearbox oil. Chip detectors are standard equipment on helicopters, where the main rotor gearbox is likewise critical to flight safety. Up until the Air Force crash, however, V-22 pilots were afforded considerable discretion in how to respond to these advisories and cautions, which do not always indicate a life-threatening problem.
The assessments were reviewed by NAVAIR but not widely shared outside the program office. AFSOC head Lt. Gen. Michael Conley alluded to this fact in the public report on the CV-22B crash when he cited inadequate program-level risk management as a contributing factor to the mishap, declaring that “safety assessments and their findings were given insufficient treatment at the program level and have been inadequately communicated to the military services, creating lack of comprehensive awareness of PRGB risks, and limiting opportunities to impose risk mitigation measures at the service or unit level.”
Subscribe to The Air CurrentThe V-22’s accident record — which includes four fatal crashes over the past two-and-a-half years — has led many people to perceive this military tiltrotor as uniquely unsafe, and its troubles as having little relevance to the rest of the aviation industry. Yet its history of inclusion-related gear failures has a direct bearing on other Bell helicopter models, while also highlighting an insidious problem that has not been fully solved in either military or civil aviation.
Inclusions are often thought of as one-off issues caused by lapses in manufacturing quality control. While this can be the case, many inclusions are byproducts of the melting process used to ensure high purity, and too small to be detected using existing inspection techniques. Such “stealth anomalies” have been responsible for gear failures in rotorcraft as well as numerous uncontained engine failures in commercial jets, including the 2016 engine failure on American Airlines flight 383. They have prompted a behind-the-scenes research effort to overcome the limitations of today’s manufacturing and inspection technology — an effort that remains ongoing.
A complex system
The frequency of gear failures on the V-22 is directly related to the fact that its complex drive system has a great many gears. The total weight of the drive system on each aircraft has been publicly given as around 3,780 pounds — more than a Toyota Camry — including two proprotor gearboxes (which account for more than 2,600 pounds or 70% of the total weight) plus tilt-axis and mid-wing gearboxes and an interconnect shafting system. X-53 gears do not make up the majority of this weight, but they account for a significant percentage of it.
The proprotor gearboxes transmit power and provide speed reduction from the Rolls-Royce AE 1107C engines to the slower-turning proprotors. Power is transferred from each engine first through an input quill, then a series of input helical gears and a bull gear to the high-speed planetary assembly. The planetary assembly is named for its resemblance to a solar system, in which multiple pinion or “planet” gears rotate around a central sun gear.
The high-speed planetary assembly transfers power through a set of splines to the low-speed planetary assembly, which provides the increase in torque and reduction in speed needed to drive the massive proprotor. The high-speed assembly has five pinion gears, and the low-speed assembly has six pinion gears, which give each assembly a measure of redundancy. Other in-flight failures and instrumented testing have validated that the gearbox can continue to function with a cracked pinion in the absence of collateral damage.
In the Air Force crash, however, at least one piece of the failed pinion gear wedged in the high-speed carrier assembly, grinding against the high-speed sun gear’s teeth until they were completely stripped. This prevented torque from being applied to the left-hand mast, resulting in a sudden loss of thrust on that side.
According to the public report on the accident, the aircraft immediately rolled rapidly to the left and turned over twice before impacting the water. Once the gearbox failed, there was nothing the pilots could have done to recover from the situation, and the impact was not survivable.
The fatal flight
The mishap aircraft, call sign GUNDAM 22, was one of two CV-22B tiltrotors that had deployed from Yokota Air Base to participate in a joint interoperability exercise in the waters between mainland Japan and Okinawa (a third Osprey, acting as a spare, followed in trail). The purpose of the exercise was to integrate U.S. special operations forces with other U.S. military units.
The pilot was the lead planner for air integration of all participants and wore two hats as aircraft commander and airborne mission commander, responsible for the command of his own aircraft as well as command of the other airborne participants in the exercise. This was a permissible but non-standard practice, and Conley later concluded that the decision to allow the pilot to perform both roles, distracting his attention from the situation inside his aircraft, was another contributing factor to the mishap.
Around 40 minutes after takeoff from a refueling stop at Marine Corps Air Station Iwakuni, the crew of GUNDAM 22 received a left-hand proprotor gearbox chip burn advisory on their control display unit, indicating that a chip detector was melting a small piece of metal by passing electrical current through the detector’s electrodes.
Tiny metal chips can result from various causes including maintenance debris and are not always consequential. Prior to the accident, the V-22 flight manual did not require that crews react immediately to a first or second chip burn advisory. If three consecutive chip burn advisories were received during a continuous flight, then crews were advised to “land as soon as practical”. That meant that extended flight was not recommended, but the landing site and duration of flight were left to the discretion of the pilot in command.
If a chip failed to burn off for three consecutive automatic chip burn attempts, then crews would receive an auditory and visual chips caution, and the landing criteria would change to “land as soon as possible”. That was defined as executing a landing at the nearest available area in which a safe landing can be made, although the determination of landing as soon as possible was left to the discretion of the pilot when flying over water.
If the chips caution was accompanied by abnormal secondary indications — such as a change in oil temperature or pressure, or a noticeable vibration — then crews were advised to “land immediately”, which over water would require a controlled ditching resulting in loss of the aircraft.
The crew of GUNDAM 22 received a second chip burn advisory 23 seconds after the first one, then a third chip burn advisory 12 minutes later. That put the aircraft in a “land as soon as practical” situation, but Air Force guidance allowed the pilot discretion in choosing whether to continue the mission. According to a cockpit audio transcript compiled by investigators, the pilot was weighing the risk reduction role that the medical personnel who were riding in the back of the aircraft would play in the military exercise, and opted to continue toward Okinawa, 300 nautical miles away over open water.
“We are going to mark the time every time [a chip burn advisory] happens to see if it increases in frequency,” the pilot told his crew. “Keep a real close eye on any secondaries and we will pull back if we need to.”
An engineer who is directly familiar with helicopter and tiltrotor transmissions told TAC that this emphasis on secondary indications was misguided. “A chip to me as a designer and engineer is extremely important,” he said. “A chip detector indication does not mean that you have to wait for a secondary indicator such as temperature or pressure. A chip detection system can stand alone to indicate a degradation of the mechanical system in a gearbox.”
He used the analogy of a broken bone that does not necessarily result in a fever. “You can break your ankle right now; your blood pressure and your temperature and your heart rate don’t show it. But you can’t walk on your ankle.”
The GUNDAM 22 crew soon received a fourth chip burn advisory. “The one time that I actually had this it was actually in Japan,” the pilot remarked. “I think it was like 100 and some chip burns in a space of like 15 minutes with no like secondaries … and when they got the sensor off it was like one tiny piece of metal, it was definitely clearly a chip, it wasn’t good, but it was like a pencil shaving just too big to burn. So, it couldn’t burn it off and it just kept touching the sensor.”
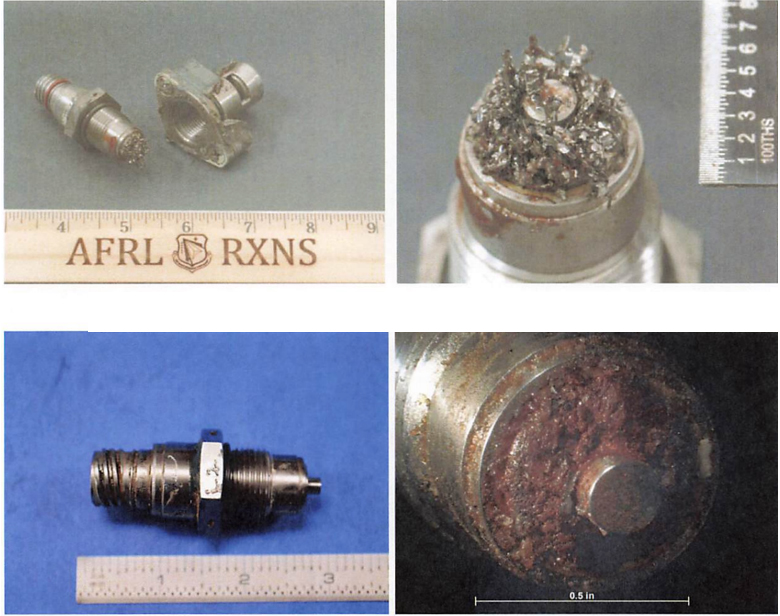
Soon came a fifth chip burn advisory, then a chips caution that put them in a “land as soon as possible” situation. By then, they were over water off the southern tip of mainland Japan. The pilot commanded a turn to an east-southeast heading toward their closest planned divert airfield, which was nearly 70 miles and 15 minutes away. “That is Yakushima unless you know of a better place,” he said.
“Nope that is closest that I have seen on the diverts,” the copilot replied. In fact, there were three closer islands with a usable runway or helipads.
The accident investigation later determined that the pinion gear had likely cracked through completely before small pieces of gear material began fracturing from the crack edges, resulting in the chip advisories. The aircraft’s vibration structural life and engine diagnostic (VSLED) system began recording vibrations five minutes before the first chip burn advisory, but that information was not available in real time to the crew, as it could only be downloaded from a ground station post-flight.
The crew continued to perceive no secondary indications of failure as they proceeded to Yakushima and briefly held for other traffic at the airfield. While holding, the crew received a “chip detector fail” advisory.
“Oh, chip detector fail that sounds more accurate,” the pilot said, laughing. “OK so now I’m less worried. … I was s***ting my pants before you guys didn’t even know. I think you could hear the strain in my voice.” In fact, what the pilot now perceived as a minor fault was the chip detector becoming so overloaded with metal flakes that it ceased to function.
The accident occurred 49 minutes after the first chip burn advisory, as the CV-22B was converting from airplane to helicopter mode for landing. Investigators noted that the conversion caused a change in torque, an increase in the rotational speed of each gear and bearing, and a change in the direction that gravity acted on the gearbox components — all factors that could have conceivably expedited the failure sequence. However, whether they actually did so is unknown, as the absolute root cause of the failure was not determined.
A stubborn problem
While investigators were unable to determine the root cause of the failure with certainty, the documented history of inclusions in X-53 gear material gave them ample reason to suspect an inclusion as a possible cause. According to a publicly releasable drive system engineering investigation report, tiny inclusions of aluminum oxide surrounded by manganese sulfide, which were within allowable size limits, were found in the failed pinion gear, and similarly sized inclusions were found in a non-failed high-speed pinion gear from the right-hand proprotor gearbox.
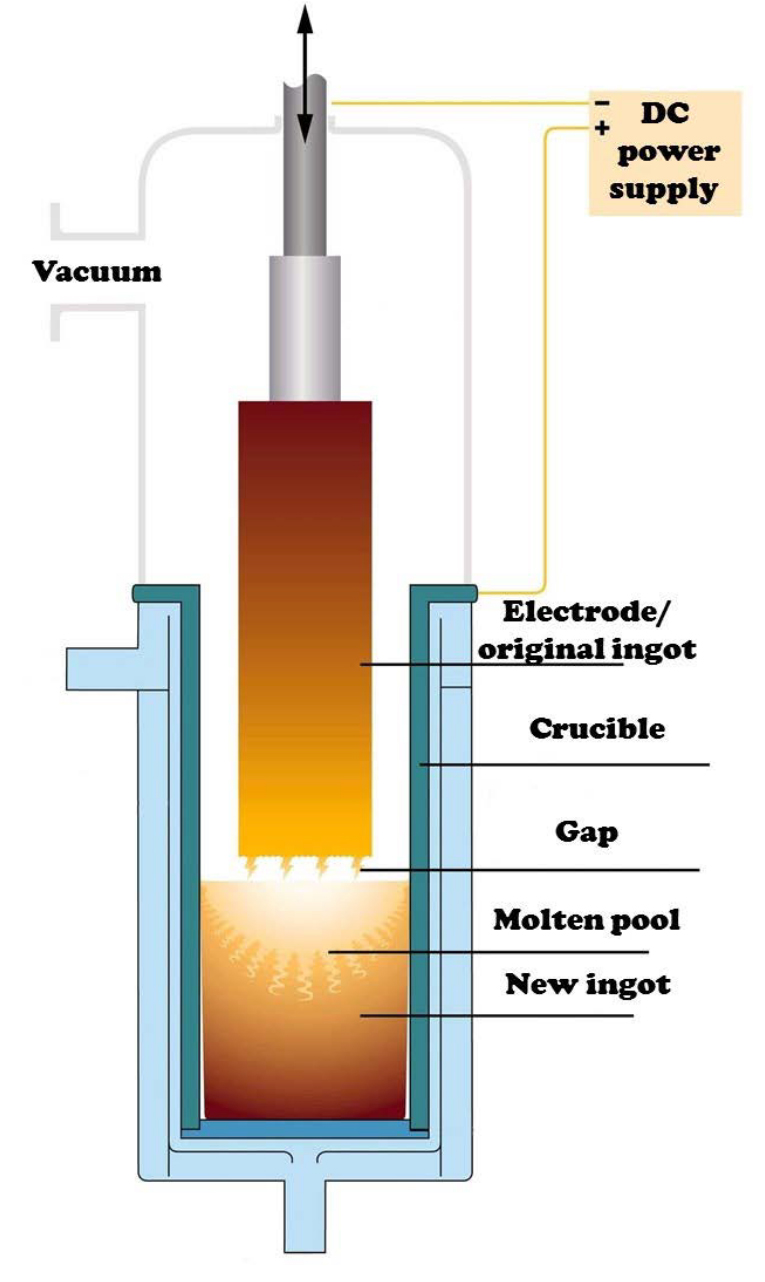
The report stated there have been a total of seven documented low-speed pinion gear failures in the V-22 that were confirmed or suspected to have been the result of inclusions, although no previous failures of a high-speed pinion gear. (The total weight of the low-speed pinion gears in a V-22 is nearly four times the weight of the high-speed pinion gears.)
“If the pinion did crack due to an inclusion, the evidence was obscured by the secondary damage,” the report states, also suggesting the possibility of a manufacturing defect such as carbide networking within the gear material, or foreign object damage from an external debris source or another component within the gearbox. Investigators did not find any evidence of carbide networks — which decrease a material’s fracture toughness, thereby increasing the number of inclusions that can initiate a crack — but that particular defect was the subject of the safety assessment conducted in 2022.
X-53 is the trade name of one of the material’s manufacturers, Universal Stainless, but it is often used as a generic name for the alloy in the same way that Kleenex is used to describe facial tissue. Bell has tapped several producers of the alloy over the years, and inclusions have been found in multiple heat lots from multiple manufacturers.
This low carbon steel was initially developed by Carpenter Steel Co. in the early 1970s in the search for a gear steel that could increase the amount of time that a gearbox could function in the event of a loss of lubrication. Testing and development work performed under the U.S. Army’s Advanced Transmission Components Investigation program starting in 1976 supported the decision to make most of the V-22’s power gears out of X-53 due to its ability to withstand higher gearbox operating temperatures than previous alloys.
X-53 is double vacuum melted, meaning it undergoes two separate melting processes in a vacuum to reduce oxygen and nitrogen content and help inhibit the formation of oxides and nitrides, which can create inclusions.
One of these processes is vacuum induction melting (VIM), which uses an induction furnace to combine the raw material and remove impurities. Another is vacuum arc remelting (VAR), which uses a direct current to melt an ingot and form a new ingot from the molten material, helping to remove dissolved gases and vaporize unwanted contaminants. The combined double-melt process is commonly referred to as VIM-VAR and is standard for aerospace components that require a high degree of cleanliness.
There are also some triple-melted alloys, used in applications including turbofan engines, which incorporate an electroslag remelting (ESR) step. This involves continuously melting an ingot through a superheated slag layer, which contains reactive elements that bind with impurities. Each additional melting step increases the cost of the final product, although the differential is typically small relative to the overall cost of an aircraft or engine.
American Airlines flight 383
Manufacturing anomalies in materials leading to component failures have always been fairly rare when compared to other accident causes, and the use of double and triple-melt alloys in conjunction with ultrasonic inspection techniques have further improved the safety and reliability of critical aerospace parts. “Nevertheless, several classes of anomalies are still routinely detected during manufacturing and some escape detection,” metallurgist John deBarbadillo wrote in a 2022 paper that explored options for reducing defects in nickel superalloys. “While the improvement in VAR product cleanliness over the past 50 years has been remarkable, we have certainly not reached the end of the road.”
According to a presentation by deBarbadillo, there is no comprehensive database for nickel rotor failures caused by metallurgical anomalies, but there were 52 nickel rotor failures associated with such anomalies between 1962 and 1998, and issues have persisted into the present day.
One high-profile example of such a failure in commercial aviation was the uncontained engine failure on American Airlines flight 383, a Boeing 767-323, in Chicago in 2016. A major investigation by the National Transportation Safety Board traced the failure to cracking initiated from a subsurface manufacturing anomaly in the GE CF6-80C2B6 turbofan engine’s high-pressure turbine (HPT) stage 2 disk.

The NTSB characterized this so-called “discrete dirty white spot” — a discontinuity in which micron-sized oxide particles were embedded — as a stealth anomaly, meaning it was likely not detectable by the ultrasonic inspection methods used during production of the HPT stage 2 disk. However, investigators found that the associated cracking developed slowly enough that it likely would have been detectable if ultrasonic methods had been required at the time of the disk’s last in-service inspection.
Shortly before the release of the NTSB’s final report, the Federal Aviation Administration issued a proposed airworthiness directive (AD) to require operators to conduct those exact ultrasonic inspections of affected GE CF6 engines’ HPT stage 1 and 2 disks. The AD went into effect in 2018 has since been expanded twice to include a larger list of affected variants.
The NTSB also recommended that the FAA establish and lead an industry group to evaluate enhanced inspection technologies for nickel alloys, and require subsurface in-service inspection techniques for all critical high-energy, life-limited rotating engine parts. Since 2019, the FAA has been engaging with two Aerospace Industries Association working groups to address the recommendations, and FAA Administrator Michael Whitaker told the NTSB in January 2024 that the agency expects to continue that work over the next few years.
Assessing risk
Inclusions that are not associated with specific fabrication process failures can be treated as randomly distributed in the material used to make parts. One materials engineer who spoke with TAC used the analogy of a single raisin in a loaf of bread the size of a car — it is unlikely that any single piece of bread will contain the raisin, but it will turn up eventually if you keep making toast.
Bell was able to associate the carbide networks in its 2022 safety assessment with a specific manufacturing process change, but the inclusions studied in its 2014 and 2020 assessments were more problematic. Supplier audits did not turn up any process issues or quality flags, and the inclusions were small enough to evade inspection. Bell was unable to identify any concrete mitigation options, although its 2014 risk assessment noted that incorporation of improved gearbox vibration monitoring had the potential to provide early detection of a slow-growing crack.
With no viable way to eliminate the inclusion hazard, Bell’s engineers were left to assess the associated risks. Air Force guidance material on risk management identifies three components of risk: severity, probability and exposure. Evaluating each of these required the engineers to make certain assumptions.
First was severity, an estimate of the likely extent of loss. This was relatively straightforward insofar as failure of certain gearbox components due to an inclusion could clearly lead to a catastrophic loss, meaning the loss of the aircraft and crew. The sun gear and bull gear were identified as critical parts because of their vital role in driving the proprotors. The planetary pinions were not identified as critical parts because of their aforementioned redundancy, but the engineers noted that if a pinion broke in two, the results would be catastrophic as large pieces would disrupt the planetary system.
The next part of the risk equation was probability, the estimate of the likelihood that a hazard will cause a loss. Part of this was determined by the base rate of inclusion-related cracks, which could be estimated by historical data. Part of it was determined by the volume of the critical gears as reflected in their weight: since the distribution of inclusions is assumed to be random, the larger the gear, the greater the likelihood it contains an inclusion.
But another part of it was guesswork: the probability that an inclusion-related crack would progress to a catastrophic failure before the pilot could get the aircraft safely on the ground. The engineers noted that it is not possible to accurately predict how long a gearbox may continue to operate following any particular gear failure — whether a few minutes or several hours — as it is dependent on the nature of the failure and the unpredictable impact of broken teeth and debris. In 2014, they settled on a factor of 50%, assuming that half the time the failure would create detectable chips and the pilot would make a safe precautionary landing.
Related: Special Report: The number at the center of an eVTOL safety debate
Multiplying these factors together gave probabilities in the range of one catastrophic event per 10 million flight hours (10-7, improbable) to greater than one event per million flight hours (10-6, remote). By way of comparison, these numerical levels of safety are equivalent to what the FAA expects of small single-engine helicopters such as the Robinson R44. Transport category helicopters and airliners are held to a much higher standard — no more than one expected catastrophic failure in a billion flight hours (10-9).
The third component of risk is exposure. Bell’s engineers introduced this concept in the 2020 and 2022 safety assessments in the context of blue water operations, which are operations in which a landing site is not available without continued flight, as is typically the case when operating over water. More parts are potentially critical in this situation because of the increased potential for a gearbox to deteriorate to failure before landing. However, the exposure to blue water operations varies by service.
In 2020, Bell’s engineers estimated that Marine and Air Force Ospreys would spend around 20% of their time in blue water operations, while Navy CMV-22B models would spend around 80%. For the Navy fleet, this higher exposure to blue water operations pushed the expected rate of catastrophic failures closer to eight per million flight hours, or almost one in 100,000 flight hours (10-5).
However, the 2022 assessment noted that an intervening risk assessment for clutch disengagement (which TAC has not seen) revised blue water exposure downward to 10% of Air Force flight time and 40% of Navy flight time. The 2022 assessment characterized the overall risk to the fleet from specific X-53 material associated with carbide networks as “medium” rather than “serious”.
Communications failure
Clearly, the results of the safety assessments were sensitive to the engineers’ assumptions, and an embedded assumption was that pilots would land promptly in response to chip indications. Yet, transcripts of interviews conducted by Air Force investigators reveal that crewmembers varied in their understanding of the significance of chips and how quickly a situation could progress to a catastrophic failure.
“Before the crash, I didn’t think prop box chips were going to change into a lost rotor system as rapidly as it seems like it might have,” one chief of standardization and evaluation told investigators in February, before the causal factors of the crash had been confirmed.
However and for whatever reasons the chain of communication broke down, it seems to have happened well over pilots’ heads. AFSOC’s Accident Investigation Board interviewed the V-22 Joint Program Office’s principal for safety, and while the public transcript of that conversation is heavily redacted, the official confirmed that system safety risk assessments conducted in 2012, 2014 and 2020 identified 1D (catastrophic-remote) serious risks, and a 2022 report identified a medium risk.
Department of Defense guidance states that user representatives must provide formal agreement before serious and high risk acceptance decisions. According to the V-22 official, as of September 2023, NAVAIR is now seeking user concurrence for catastrophic medium level risks as well.
“Do you know if any acceptances were completed for the ’14 and [’20 1D] serious risks with U.S. Air Force?” an investigator asked.
“No, I do not,” the principal for safety replied. “Those risks were not processed.”
Moving forward
NAVAIR grounded the V-22 fleet on Dec. 6, 2023, once it became apparent that the Air Force CV-22B crash in Japan was potentially caused by a material failure. The fleet returned to service three months later, on March 8.
Testifying in the U.S. House of Representatives on June 12, Vice Admiral Carl Chebi, commander of NAVAIR, said the probable root cause of the mishap was “a catastrophic aircraft material failure that we have never seen before in the V-22 program.”
Chebi said NAVAIR worked in coordination with the Marines, Navy and Air Force to develop “a path to allow for a return to restricted flight operations through implementation of specific controls.” He cited aircrew briefings on the causal factors of the mishap, aircraft logbook reviews and serial number verification of safety critical life-limited components, V-22 ground turns to verify proper drivetrain operation, mission-planning factors to limit the flight time required to land at a divert airfield and modified emergency procedures for the aircrew.
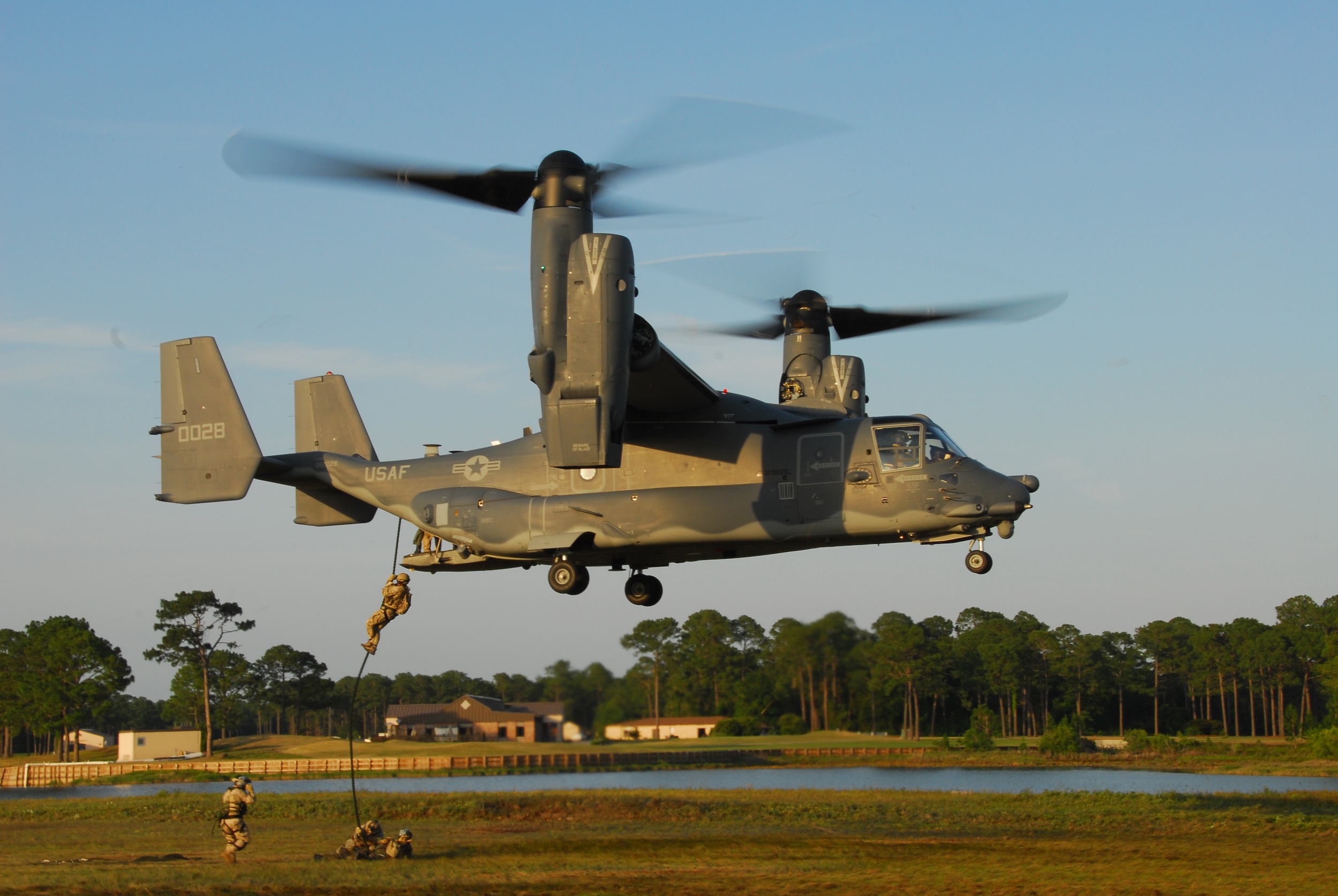
AFSOC’s Lt. Gen. Conley told reporters that crews are now directed to land as soon as practical on a first chip burn indication and as soon as possible on the second, and are limited to operating within 30 minutes of a landing location. A spokesperson for the command told TAC that AFSOC is examining changes as a result of the accident including “how airborne mission commanders are trained, determination of land as soon as practical and land as soon as possible, and finally, possible force structure change.”
Meanwhile, Chebi told Congress, “We are methodically looking at material and non-material changes that we can make to allow for a full mission set without controls in place. I will not certify the V-22 to return to unrestricted flight operations until I am satisfied that we have sufficiently addressed the issues that may affect the safety of the aircraft. Based on the data that I have today, I’m expecting that this will not occur before mid-2025.”
On Aug. 1, TAC reached out to NAVAIR’s PMA-275 V-22 Joint Program Office for comment after reporting through July confirmed that the CV-22B gear failure was related to a manufacturing defect. In a statement, a PMA-275 spokesperson said at the time, “The maintenance and procedural changes that have been implemented across the V-22 enterprise directly address the Safety Investigation Board (SIB) and Accident Investigation Board (AIB) findings to mitigate the risk of this materiel failure.”
Contacted again this week regarding the safety assessments reviewed by TAC, the PMA-275 spokesperson did not immediately provide comment.
Although the spokesperson didn’t mention it, NAVAIR has actually been working on the problem of inclusions for some time. In 2021, it solicited for Small Business Innovation Research (SBIR) Topic Number N212-108, for proposals to design and develop a steel processing method to “dramatically reduce the inclusion content of steel bar stock for current gear material X-53 double vacuum melt (AMS 6308) beyond levels currently available commercially in steel intended for use in aerospace-level gear-and-bearing components.”
The call for proposals noted that “the Navy occasionally faces issues with inclusions in aerospace components made from the current gear material X-53 double vacuum melt (AMS 6308). Developing a cost-neutral manufacturing technology that would allow higher grade steel material with dramatically lower inclusion content would increase fatigue life, improve safety, and lower sustainment costs for a steel component.”
A contract was awarded to Oregon-based Ampere Scientific, which has developed two complementary tools to help reduce inclusion defects during VAR processing. One of them is a sensor system called VARmetric, which senses the distribution of the arc (an indicator of melt quality) during the vacuum arc remelting process. Another is ARControl, which tailors the heat flux in response to monitoring data to improve melt quality.
According to Ampere Scientific CEO Paul King, the company has demonstrated its technology for X-53 in a laboratory setting and is now preparing for industrial trials. He said they expect to have results from the first set of industrial trials later this fall or early winter.
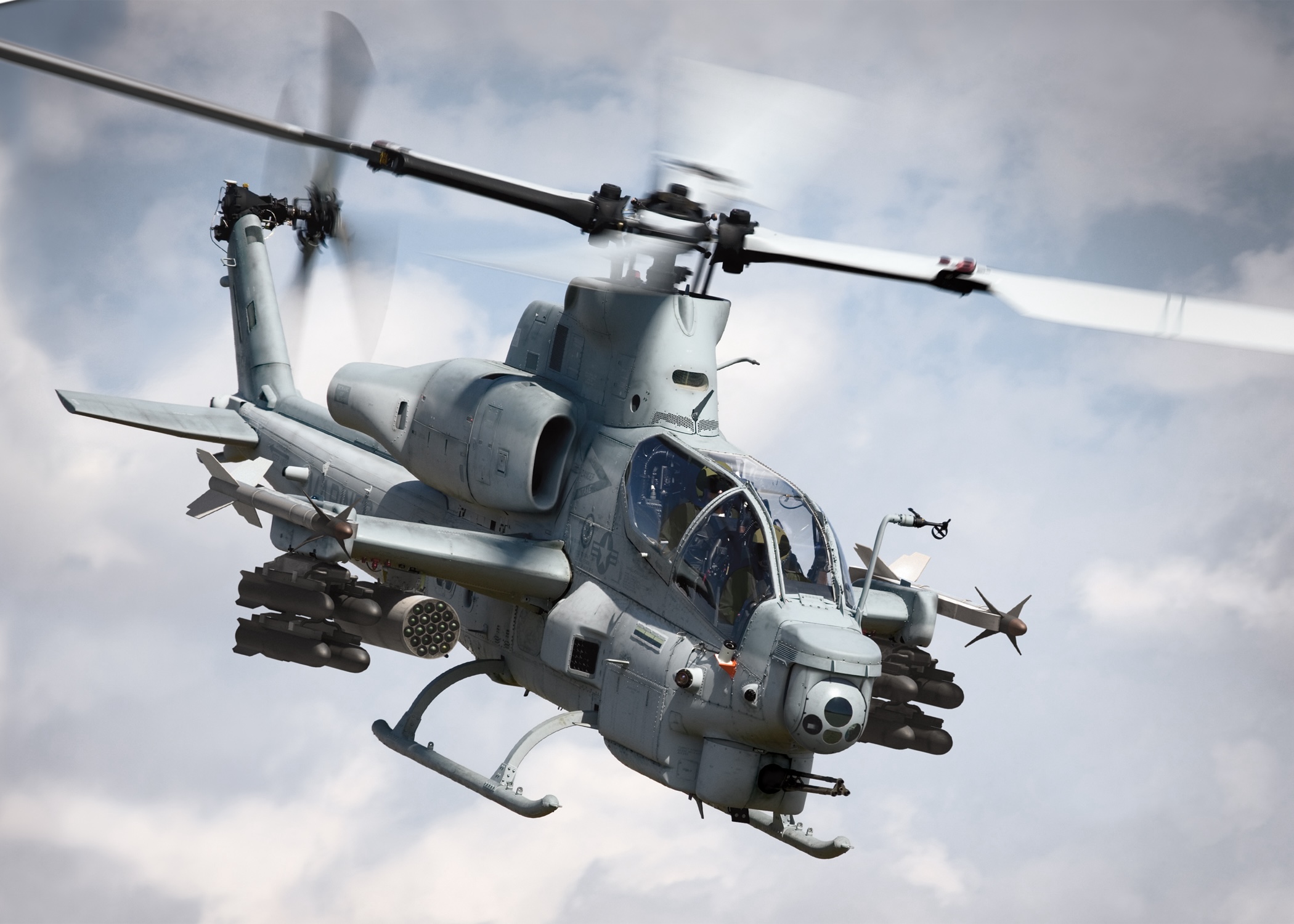
While the safety assessments reviewed by TAC were prepared specifically for the V-22 program, they allude to other aircraft potentially impacted by the same problem. The 2014 safety assessment notes that X-53 steel is used in the H-1 main rotor gearbox (impacting AH-1Z Viper and UH-1Y Venom helicopters) as well as “several other Bell models.” The 2014 report also mentions three Model 407 input gears made from X-53 which had cracked due to inclusions. The 2022 assessment refers to the H-1 program as having a 1E (catastrophic-improbable) risk.
A Bell spokesperson declined to comment and referred all questions related to the X-53 safety assessments to NAVAIR. However, in a statement following the Aug. 1 release of the final CV-22B mishap report, Bell Boeing said, “The people of Bell Boeing remain saddened by the loss of eight airmen in this tragic accident and we continue to extend our sympathies to the crew’s families and loved ones.
“As safety is our top priority, Bell Boeing will continue to work closely with the DOD and all operators of the Osprey aircraft to ensure the continued safe operation of the V-22 fleet.”
Jon Ostrower and Will Guisbond also contributed to this article.
Write to Elan Head at elan@theaircurrent.com
Subscribe to The Air CurrentSubscribe to Continue Reading
Our award-winning aerospace reporting combines the highest standards of journalism with the level of technical detail and rigor expected by a sophisticated industry audience.
- Exclusive reporting and analysis on the strategy and technology of flying
- Full access to our archive of industry intelligence
- We respect your time; everything we publish earns your attention