Air safety reporting by The Air Current is provided without a subscription as a public service. Please subscribe to gain full access to our all scoops, in-depth reporting and analyses.
The Tuesday evening collision between a landing Japan Airlines flight and a Japan Coast Guard (JCG) Dash 8-300 is going to form a new chapter in the history of contemporary commercial aircraft safety — providing critical lessons for the latest generation of all new aircraft and illustrating a successful evacuation that promises to establish a baseline for crew performance.
The 5:47 pm local time accident at Tokyo’s Haneda Airport resulted in the deaths of five members of the JCG aboard a De Havilland Dash 8-300 configured for maritime patrol operations — just a day after a magnitude 7.5 earthquake struck Japan, resulting in tsunami waves hitting the country’s western coast. Aboard the two-year old Airbus A350-900, all 368 passengers and 12 crew members survived virtually unscathed.
This accident represents the first hull loss for the A350 and the nearly 1,800 next-generation carbon fiber composite airliners from Boeing and Airbus. While the investigation will center on the sequence of events leading up to the collision — including notification of inoperative stop bar lights buried in a list of coded NOTAMs and a hold short instruction that the JCG crew acknowledged but failed to comply with — the accident itself provides an opportunity to examine the passenger and crew actions during the evacuation, the airport rescue response and the ensuing fire that consumed the jetliner’s majority carbon fiber composite structure.
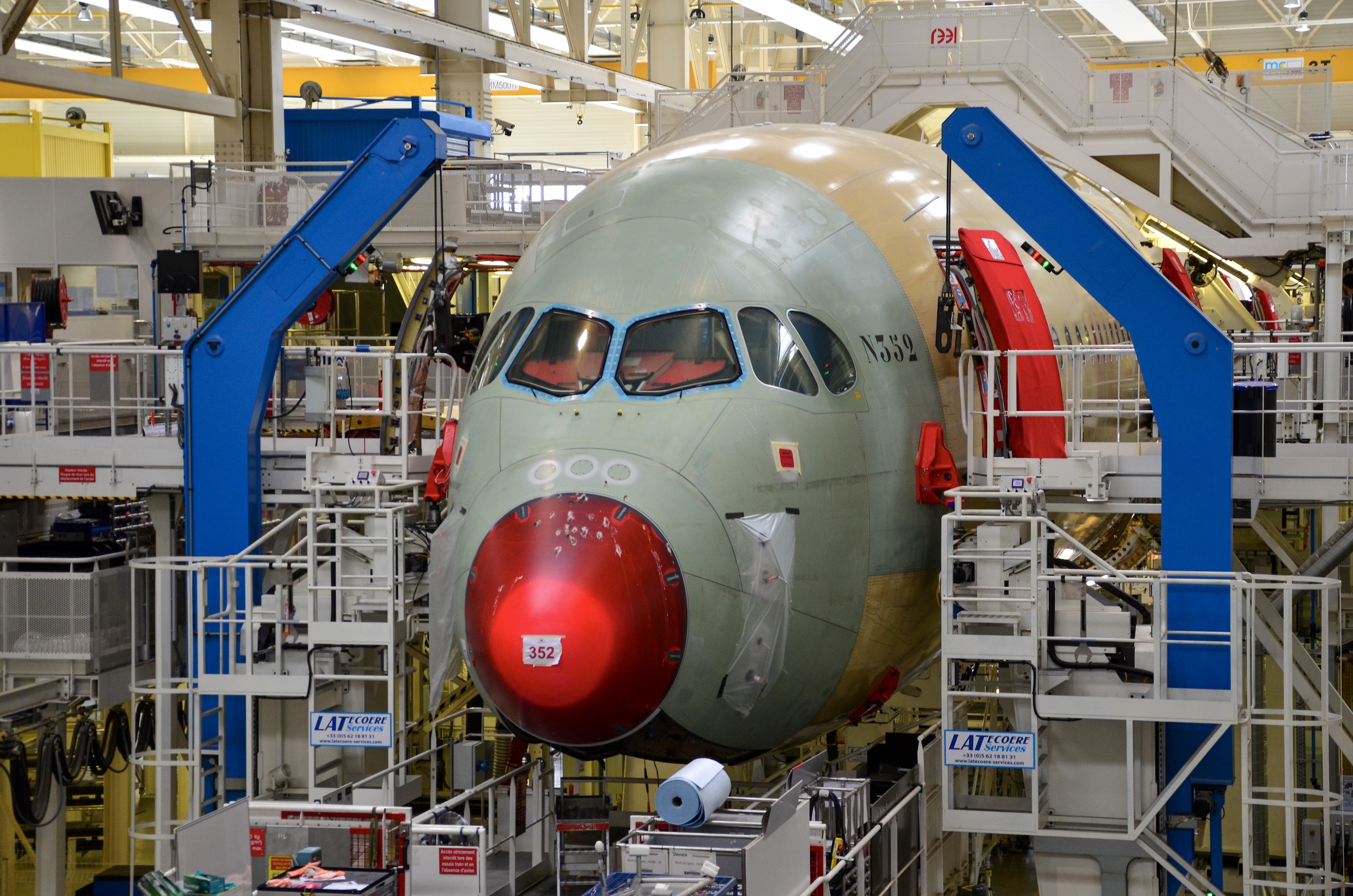
It’s been just over 20 years since Boeing committed to building the 787, a technological turning point that brought carbon fiber to widespread use in both fuselages and wings — tipping the balance of composite material to be the majority of materials used for aircraft construction. Airbus followed three years later with the clean-sheet A350. Both take different approaches to their implementation of major structural components: the 787 employs a complex monolithic barrel design to reduce weight with carbon fiber reinforced polymers, while the A350 has carbon panels built up into the cylindrical fuselage sections coupled with aluminum lithium around the cockpit, more reminiscent of legacy aluminum aircraft. Both produce huge efficiencies for their operators.
A swift exit
In addition to the structural attributes of both aircraft, considerable advancements have been made in aircraft safety systems for use in the air and on the ground: evacuation technology, environmental control systems, fuel tank inerting, smoke mitigation and fire suppression systems all intended to give the occupants sufficient time to evacuate the aircraft. All large commercial aircraft are required to show (by analysis, partial or full-scale test) that they can be evacuated within 90 seconds with half the exits unavailable. The A350-900 is certified up to 440 passengers.
In the case of the JAL A350-900 (an aircraft configured with 391 seats for domestic flying) only three of the eight slides were deployed because of the dangerous conditions around the remaining exits. JAL noted that the public announcement and intercom systems were inoperative after the crash, forcing the crew to use megaphones to direct the passengers.
The yet to be released preliminary report from Japanese and European investigators is likely to provide clarity on the timestamps of key events immediately after the collision. Notably, the airline reported that the last crew member left the A350 some 18 minutes after the initial crash, though it is not clear how soon after the accident the evacuation was initiated. That’s far beyond the 90-second requirement.
“You can look at it two ways: Why did it take so long? 18 minutes is unacceptable; or: Even with 18 minutes taking too long, everyone onboard was saved,” Cristian Sutter, a cabin design specialist for British Airways told the Wall Street Journal, noting that the pace a fire spreads across an aircraft is different in every incident. “In a different kind of accident, that time might not be there.”
“The JAL cabin crew should be highly commended for their textbook evacuation,” according to a report from Reuters that quoted an Airbus spokesperson. Airbus conducted partial evacuation tests during the A350’s development.
Perhaps crucially, footage from the crash site showed passengers without their carry-on luggage coming off the aircraft. JAL’s safety video explicitly illustrates the risk of doing so, far more than many carriers that have made their demonstrations a vehicle for marketing, as well as safety.

The absence of carry-ons is a notable contrast to other incidents — including the evacuation of an American Airlines 767-300ER at Chicago’s O’Hare Airport in 2016. Some passengers during the jet’s evacuation during an uncontained engine failure on the takeoff roll explicitly disregarded cabin crew instructions to leave their luggage. The aircraft sustained significant damage, including the collapse of much of the right wing.
That spawned a 2018 safety recommendation from the NTSB urging the FAA to “conduct research to (1) measure and evaluate the effects of carry-on baggage on passenger deplaning times and safety during an emergency evacuation and (2) identify effective countermeasures to reduce any determined risks, and implement the countermeasures.”
The 2018 FAA reauthorization explicitly called for a congressionally mandated study within a year, though the agency did not issue a formal report of its findings until March 2022. The JAL evacuation is likely to add a further spotlight to the missing real-world conditions — including interference from carry-on baggage and challenges facing passengers with disabilities — absent from U.S. regulator tests that drew criticism from Congressional and labor officials.
In July 2023, FAA acknowledged NTSB concerns. Responding to its safety recommendation, the agency noted it was working with the University of Greenwich in England to plan a study and develop “test methods to derive key modeling parameters using live test subjects, such as the time it takes to retrieve carry-on bags and the speed of movement throughout the aircraft when carrying bags.” It promised an update by May 31, 2024.
Carbon fiber immolation
Immediately following the JAL evacuation, the A350’s body was almost completely consumed by fire, creating a precedent-setting burn seen on raw video footage that rapidly propagated across the aircraft outer structure and skin, leaving the glowing inner frame of the fuselage. The fire took more than six hours to fully extinguish.
There has only been limited data in the real world to date about how composite aircraft structures respond to fire, including several examples from military aviation like the 2008 B-2 crash in Guam. Thus, this most recent incident just provided the aircraft design, fire rescue and regulatory communities with a massive trove of new data on the crashworthiness of carbon fiber, including how (and quickly) the composite structure burns in a full-scale environment after other life-preserving mitigations are felled.
In the case of the emergency locator transmitter (ELT) fire aboard an Ethiopian Airlines Boeing 787-8 at Heathrow in 2013, the resulting inquiry by U.K. officials noted the carbon fiber itself was a causal factor. “The resin in the composite material provided fuel for the fire, allowing a slow-burning fire to become established in the fuselage crown, which continued to propagate from the ELT location even after the energy from the battery thermal runaway was exhausted,” according to the U.K. Air Accidents Investigation Branch report.
Yet, Emile Greenhalgh, professor of composite material at Imperial College in London, said “unlike aluminum alloys, polymer composites form a char layer which can slow down the progress of the fire (giving the passengers more time to exit the aircraft). So, although composites start to burn at lower temperatures than metallics, they have important beneficial mechanisms when exposed to fire,” according to a post on LinkedIn.
The advanced aircraft of the 2010s, the A350 and 787 (and the similarly designed A220) are the latest to benefit from decades of advancements driven by over-engineering and stringent regulatory requirements born from earlier tragedies.
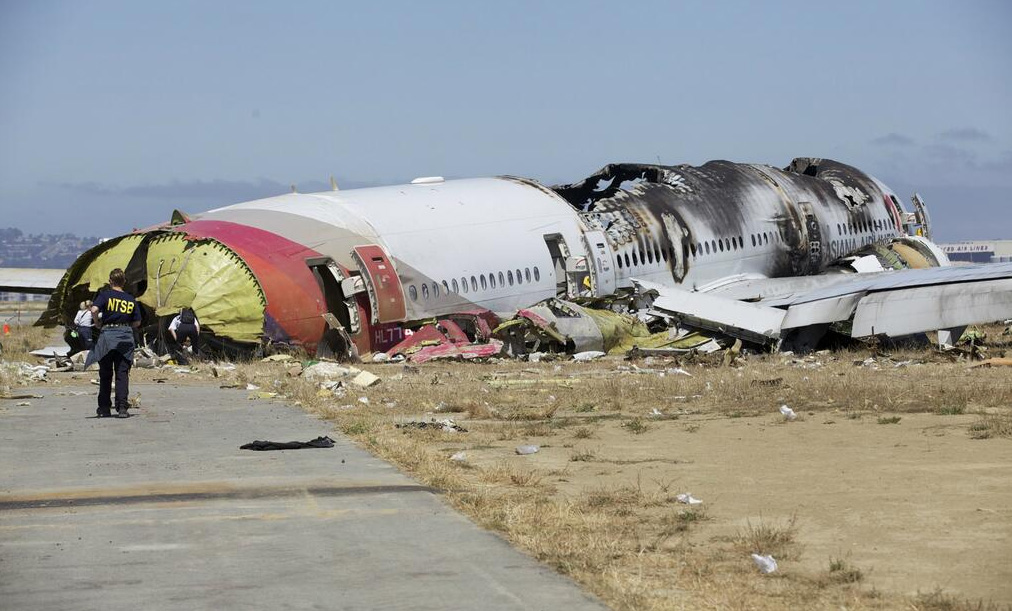
But well before Tuesday’s accident, structural and systems resilience of the new aircraft fielded over the last two and half decades have had spectacular real-world demonstrations: a failed Emirates go around in Dubai of a 777-300 in August 2016, an airborne uncontained engine failure of a Qantas A380 in 2009, a fuel starvation-caused belly landing of a British Airways 777-200ER at Heathrow in 2008, a cartwheeling crash of an Asiana 777-200ER in San Francisco in 2013, the Toronto crash in bad weather of an Air France A340-300 in 2005. All but the A380 resulted in the loss of the aircraft, and across all of these accidents only two passengers did not survive as a result of the initial crash.
Those outcomes were the result of seats that can withstand 16 Gs of force, less flammable cabin materials, as well as other advancements in systems integration and redundancy born from accidents of the 1980s and 1990s. The JAL accident strikingly illustrates the sum total of all the factors that together prevented this accident from becoming a far greater tragedy. And it will provide tangible data on which the next generation of accidents can be lessened or avoided altogether.
Write to Jon Ostrower at jon@theaircurrent.com
Subscribe to Continue Reading
Our award-winning aerospace reporting combines the highest standards of journalism with the level of technical detail and rigor expected by a sophisticated industry audience.
- Exclusive reporting and analysis on the strategy and technology of flying
- Full access to our archive of industry intelligence
- We respect your time; everything we publish earns your attention