Log-in here if you’re already a subscriber
Air safety reporting by The Air Current is provided without a subscription as a public service. Please subscribe to gain full access to our all scoops, in-depth reporting and analyses.
The Bell Boeing V-22 Osprey fleet will continue to face a “serious” risk of catastrophic failure due to flawed transmission gears even after the implementation of new risk mitigation controls involving manufacturing improvements and flight hour thresholds for the tiltrotor, according to a nonpublic system safety risk assessment by Naval Air Systems Command (NAVAIR) reviewed by The Air Current.
The U.S. Marine Corps, Navy and Air Force temporarily paused operations of the V-22 in early December after it became apparent that the November near-crash of a CV-22B at Cannon Air Force Base in New Mexico was caused by the failure of a critical gear due to an inclusion — an impurity in the X-53 steel alloy used to make the gears that creates a weak point in the metal. A similar inclusion-related gear failure was responsible for the November 2023 crash of another Air Force CV-22B near Yakushima Island, Japan, which killed all eight people on board.
Related: Flawed metal and failed communication: Breaking down the Air Force’s fatal Osprey crash
As The Air Current detailed in a special report in August 2024, the investigation into the Japan crash faulted the V-22 program for not communicating the findings of previous inclusion-related safety assessments to operators of the aircraft. This time around, the military is resuming V-22 flight operations with eyes wide open, aware that the estimated frequency of catastrophic failures due to inclusions is as high as seven per million flight hours — and that even planned improvements to the gear manufacturing process are unlikely to reduce this figure below the threshold of one per million flight hours that is used to categorize serious risk. Both rates are well outside of what the military typically requires for airworthiness certification, which is no more than one catastrophic failure per 10 million flight hours.
NAVAIR did not immediately respond to a request for comment.
NAVAIR on Dec. 20 issued a fleet bulletin directing operators to verify the flight hours on each V-22 proprotor gearbox before further flight. Aircraft with proprotor gearboxes exceeding a predetermined flight hour threshold were cleared to resume operations in accordance with risk controls that were implemented in March 2024 as a result of the Japan crash. Aircraft with proprotor gearboxes that had logged fewer flight hours than the threshold were subject to additional restrictions that were not publicly disclosed.
NAVAIR did not explain the rationale behind the flight hour threshold in its public statement on the bulletin. However, the nonpublic safety assessment reviewed by TAC, which was shared with operators and dated Dec. 17, 2024, indicates that the majority of the inclusion-related failures that have occurred to date have happened early in the life of the gears. It is believed that gears that surpass the flight hour threshold without experiencing problems are less likely to contain inclusions, which are not detectable using existing inspection techniques.
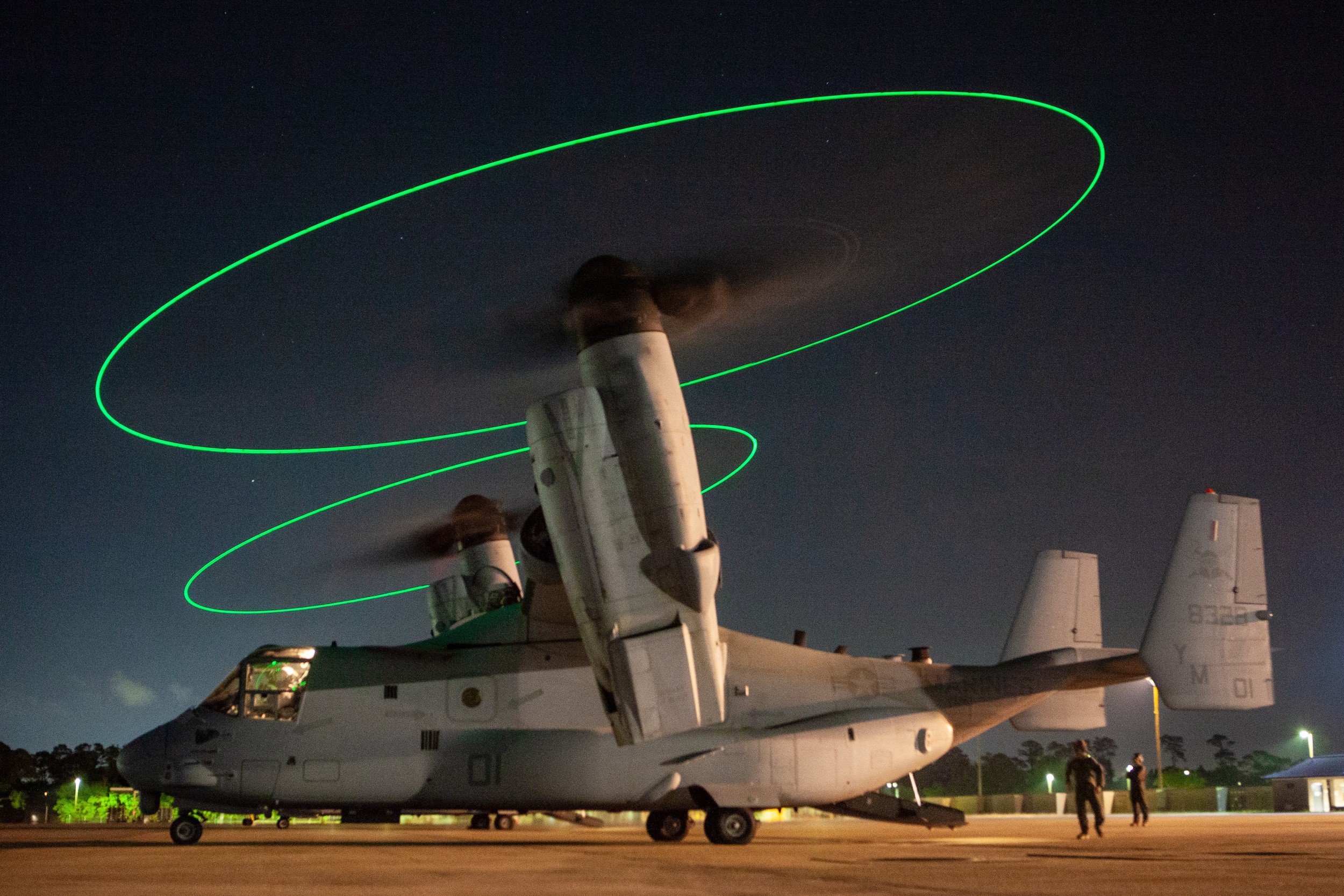
Because NAVAIR has indicated that there are operational security concerns associated with revealing the specific flight hour threshold, TAC is not disclosing the figure, but understands it to be higher than the number of flight hours logged by 90% of the V-22 gears whose failures have been attributed to inclusions. The remaining 10% of failures occurred above the flight hour threshold, suggesting that implementing the threshold will reduce but not entirely eliminate the risk posed by inclusions.
Notably, the safety assessment indicates that there have been 20 such failures in the approximately 800,000 flight hours logged by the V-22 fleet to date. This figure is higher than previously reported and includes two inclusion-related failures in the six months prior to the fatal crash in Japan, neither of which had a catastrophic outcome.
Although the Japan crash, which was determined to have been caused by the failure of a high-speed planetary pinion gear, is the only catastrophic V-22 accident that has resulted from an inclusion to date, the safety assessment notes that there were two “near miss” events involving input idler helical gears with the potential to be catastrophic. One of these was the November incident at Cannon Air Force Base, which occurred shortly before touchdown but resulted in a non-recoverable in-flight engine shutdown and proprotor gearbox case rupture.
The other helical gear failure occurred during a second green run after having passed its initial green run, a post-assembly test performed at the factory to break in gearbox components before installation on an aircraft. Due to a fire at the Bell Drives System Center in Grand Prairie, Texas in 2020, the associated proprotor gearbox was disassembled, cleaned, inspected, rebuilt and subjected to a second test. “It is by happenstance that this gear was not installed on aircraft following its first successful green run,” the safety assessment states. “Had it been installed, a catastrophic gear failure could have occurred on-wing, potentially resulting in loss of personnel/aircraft.”
Critical assumptions
The safety assessment underscores the incredible complexity of the V-22’s drive system, which includes 41 critical and primary drive gears made from the X-53 alloy.
Seven of the 20 documented inclusion failures involved low-speed planetary pinion gears, which are part of the low-speed planetary assembly in each proprotor gearbox that provides the increase in torque and reduction in speed necessary to drive the proprotor. Although all of these gears cracked through fully, none of them caused serious damage to the adjacent drive system components, and the remaining five pinion gears in each assembly carried the load. All of them produced metal chips that activated magnetic chip detectors in the gearbox system, providing flight crews with a cockpit indication of a possible failure. One aircraft flew successfully for 39 minutes after the crew received an indication of chips in the gearbox oil, and ground testing has demonstrated that a V-22 can fly for more than eight hours with a cracked low-speed pinion gear.
Because the adjacent high-speed planetary assembly also contains multiple pinion gears (five in this case), Bell engineers originally assumed that it was similarly redundant. As a result, according to the safety assessment, it was not designed to the same flaw tolerance specifications as known critical gears including the bull and low speed sun gears.
In the Japan crash, the crew flew for 49 minutes from the time of the first chip burn advisory until the left-hand proprotor gearbox failed catastrophically as the aircraft was converting from airplane to helicopter mode for landing. Investigators determined that a cracked high-speed pinion gear had broken into pieces that stripped the teeth from the high-speed sun gear and prevented torque from being delivered to the proprotor. Subsequent ground testing showed that an inclusion-induced crack in a high-speed pinion gear could lead to a catastrophic failure in as little as five minutes, leading engineers to reclassify that part as critical.
Inclusions are assumed to be randomly distributed in the X-53 raw material, with one materials engineer previously describing them to TAC as analogous to a single raisin in a loaf of bread the size of a car. The safety assessment calculates the likelihood of an associated catastrophic failure based on the number of critical gear sections and the weight of the X-53 they contain. The assessment gives an average catastrophic failure rate estimate of 7.45 x 10-6, or a little over seven failures per million flight hours. This is considered to be an upper bound for the failure rate, given that the observed failure rate is 3.75 x 10-6 when including the two near-miss events.
Related: Special Report: The number at the center of an eVTOL safety debate
By comparison, transport category civil aircraft are certified to an expected failure rate of no greater than 1 x 10-9, or one catastrophic failure per billion flight hours, and even small piston-powered helicopters are required to have an expected catastrophic failure rate of no more than 1 x 10-6. A Department of Defense handbook on airworthiness certification criteria specifies a numerical safety level of 1 x 10-7, but one knowledgeable engineer who spoke with TAC said that military aircraft are commonly designed to higher than this minimum standard unless weight is an issue. However, as TAC has previously explored in depth, these numerical safety analyses are only as good as their assumptions around failure modes and the loads that a component will experience in service.
Ambiguous warnings
Of the 13 components in the V-22 proprotor gearbox that have previously been identified by NAVAIR as single points of failure (some of which contain multiple gears), nine of these may shed metal chips into the gearbox oil as part of failure progression. Each proprotor gearbox has three chip detectors that can automatically “burn off” very small pieces of metal using electric current, and four chip collectors in the form of magnetic plugs.
If a chip detector is able to successfully burn off a piece of debris, pilots will receive a chip burn advisory message in the cockpit. In the event of three consecutive failed burn attempts, a chips caution will post along with an audible tone and caution light.
Prior to the crash in Japan, the Air Force advised its flight crews to “land as soon as practical” if they received three chip burn advisories during a continuous flight. If they received a chips caution, they were advised to “land as soon as possible” at the nearest available area in which a safe landing could be made, with that determination left to the discretion of the pilot when flying over water.
Following the crash, that criteria was tightened up considerably, with crews directed to land as soon as practical on a first chip burn indication and as soon as possible on the second. They were also limited to operating within 30 minutes of a landing location.
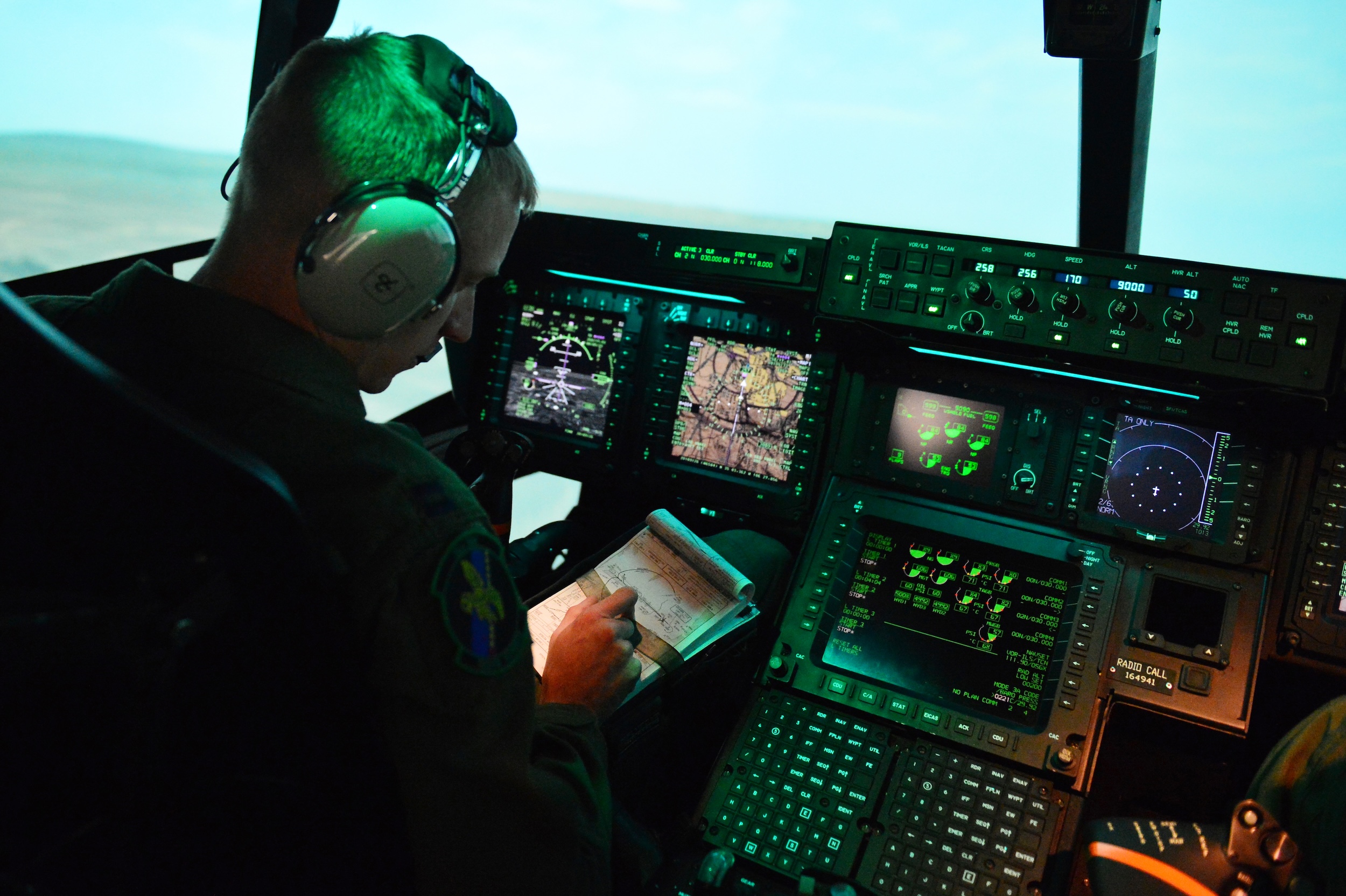
An earlier NAVAIR safety assessment initiated in January 2024 that was also reviewed by TAC shows that since 2005, there have been more than 600 proprotor gearbox chips caution events recorded in available flight data, 40% of which resulted in proprotor gearbox removals following evaluation of magnetic plug debris. There were also more than 1,300 chip burn advisory events, 20% of which were linked to removals.
However, in the five-year period from 2019 to 2023, only 2% of chip-related proprotor gearbox removals were due to inclusions, underscoring the ambiguity of the chip detection system, which does not always indicate an imminent failure. Even among the low-time V-22 gearboxes that are at higher risk for inclusions, the January safety assessment indicates that the leading cause for gearbox removals is spalling, or flaking, of the planetary pinion bearing assembly due to a separate chip-producing failure mode that is slow to progress and already being addressed through engineering changes.
Moving to triple melt
As previously detailed by TAC, the X-53 steel alloy used in the V-22 and some other Bell helicopter models is subjected to a double vacuum melt process that includes vacuum induction melting (VIM) and vacuum arc remelting (VAR), both intended to increase the purity of the alloy. The combined double melt process is commonly referred to as VIM-VAR and is the standard for aerospace components that require a high degree of cleanliness for safety.
While it is impossible to completely eliminate inclusions using existing manufacturing techniques, there are triple melt processes that can further reduce the likelihood of impurities. According to the December safety assessment, in the aftermath of the Japan crash, the V-22 Joint Program Office has chosen to implement triple melt VIM-VAR-VAR on all X-53 proprotor gearbox components, with depot-level incorporation beginning in the summer of 2025.
The assessment indicates that the triple melt process is expected to result in an 85% overall reduction in the likelihood of inclusion-related failures. While significant, this would not be sufficient to reduce the expected failure rate below one in a million flight hours.
“Regardless of the options pursued, the risk will remain I-D, Serious risk for the foreseeable future,” the assessment states (where “I” refers to a “catastrophic” event and “D” to a “remote” probability of greater than 1 x 10-6 in the military’s system safety hazard risk index matrix).
Nevertheless, the V-22’s operators have evidently decided that this risk is acceptable for the aircraft’s unique operational benefits, as the V-22 can fly faster and farther than conventional helicopters while still being able to land in confined spaces. The safety assessment received signed acknowledgments from Marine, Air Force and Navy commanders.
“The V-22 plays an integral role in supporting our nation’s defense,” NAVAIR stated in a Dec. 20 press release announcing the aircraft’s return to service. “Returning these vital assets to flight is critical to supporting our nation’s interests.”
Write to Elan Head at elan@theaircurrent.com
Subscribe to Continue Reading
Our award-winning aerospace reporting combines the highest standards of journalism with the level of technical detail and rigor expected by a sophisticated industry audience.
- Exclusive reporting and analysis on the strategy and technology of flying
- Full access to our archive of industry intelligence
- We respect your time; everything we publish earns your attention