Most of the certification process for electric vertical take-off and landing aircraft is aimed at preventing these novel vehicles from crashing. But a significant portion of it concerns what happens if and when they do.
Historically, occupant safety wasn’t a top priority for the civil VTOL (which is to say helicopter) industry. The Federal Aviation Administration adopted dynamic crashworthiness standards for helicopters in 1989, and stringent fuel system crash resistance requirements in 1994. But because most helicopters had initial type certificates approved before those dates, they were not required to comply with the standards, and occupants continued to die in preventable post-crash fires.
It wasn’t until one especially high-profile fatal accident was captured on video that Congress mandated crash-resistant fuel systems in all new-build helicopters starting in 2020, and the European Union Aviation Safety Agency is now contemplating similar or expanded requirements. (Compliance with dynamic crashworthiness standards has yet to be addressed.)
Related: An old aerodynamic problem could pose a new challenge for eVTOL aircraft
As new types of aircraft, eVTOLs will have to meet the latest standards for occupant protection, but there’s one sticking point: These standards don’t already exist. While requirements for conventional airplanes and helicopters are well defined, regulators are still in the process of establishing what will be required to demonstrate crash safety in fully electric aircraft.
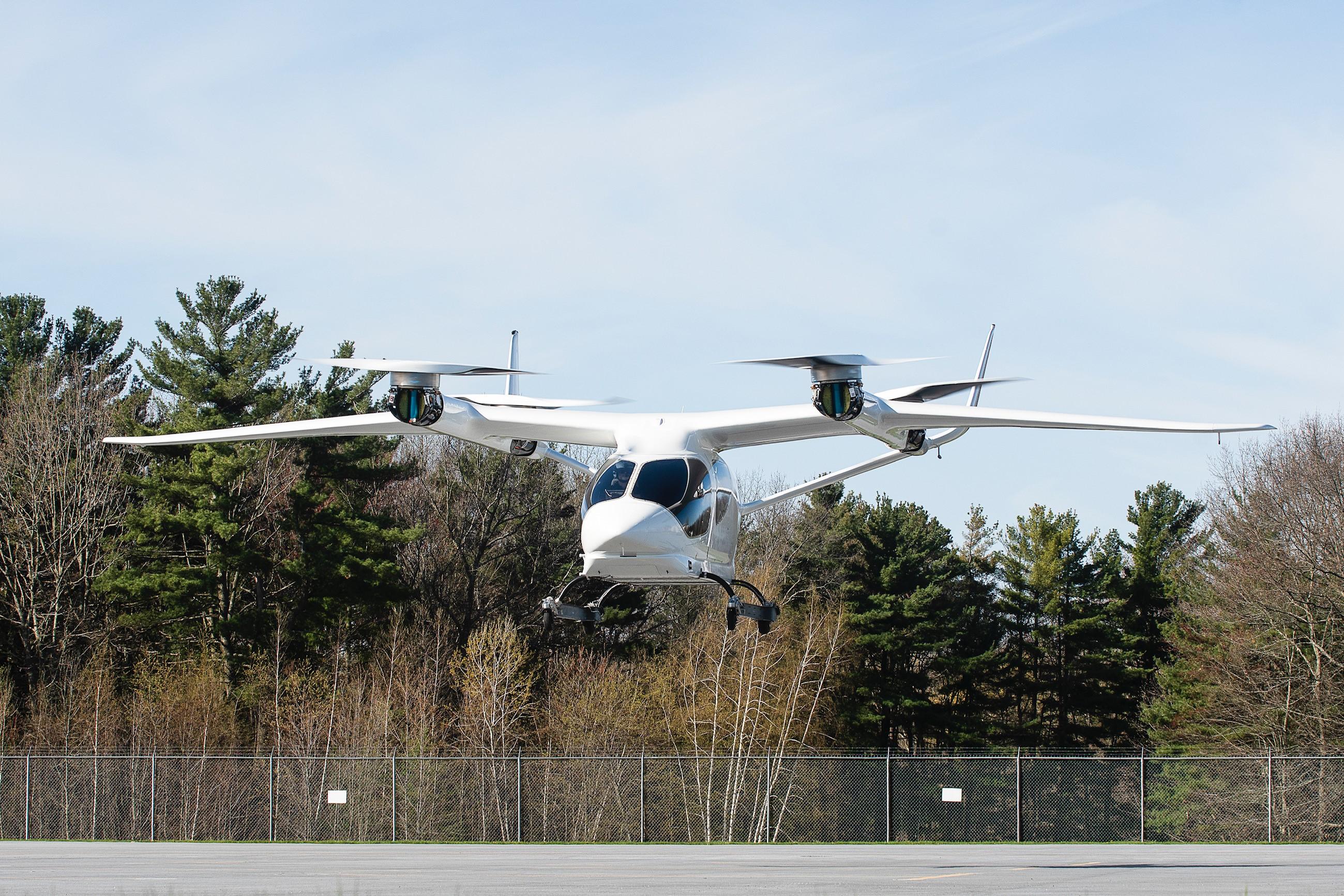
When it comes to preventing post-crash fires in eVTOLs, both the FAA and EASA are drawing heavily from the existing prescriptive standards for helicopters, which typically crash with more vertical velocity than airplanes. Perhaps the most demanding of these standards is to show that each fuel tank can, when full, survive a 50-foot drop onto a hard surface. In published means of compliance for its Special Condition VTOL, EASA has transposed the existing drop test requirements more or less directly onto “energy storage systems” — i.e. batteries — and the FAA is also using this approach as a baseline means of compliance.
Consequently, eVTOL developers have been designing their battery packs to withstand such an impact and conducting internal testing to validate their designs. But a milestone was reached on December 7, when Vermont-based eVTOL developer Beta Technologies collaborated with the FAA and National Institute for Aviation Research (NIAR) at Wichita State University in Kansas on a 50-foot drop test of one of Beta’s full-scale, 800V battery packs. A video and details of the test were released a couple of weeks later, providing the public with their first insight into the battery drop testing process.
The cylindrical battery cells were charged to around 95 percent for the test, which was reportedly a success, with no significant damage at the cell or pack level. While thermal runaway resulting from impact damage is an obvious concern for eVTOL batteries, it is also important that occupants and first responders be protected from high-voltage discharge.
The participants said the results will help validate NIAR’s simulation methods for modeling the effect of the drop test on battery systems, in addition to assisting the FAA in determining future test requirements and means of compliance. The public nature of the test may help reassure skeptics that batteries aren’t necessarily more hazardous in a crash than are tanks of jet fuel; rather, they are engineered systems that can be designed with appropriate safeguards.
Beta’s Alia eVTOL has all of its batteries in the belly of the aircraft, but other designs have distributed battery packs; for example, Joby Aviation’s tiltprop eVTOL has its batteries in the main wing and forward nacelles. Current drop test requirements specify that the energy storage system should be enclosed in a surrounding structure representative of the installation, and indeed, Joby has been encasing its batteries in representative sections of nacelles for its own, in-house drop tests.
Simultaneously, eVTOL developers need to be thinking about how their battery systems will interact with the crashworthy seats and structures required to protect occupants from impacts. Also last month, NASA released video of its own full-scale crash test of a six-passenger eVTOL concept vehicle with an overhead mass designed to represent the wing structure, rotor and battery.
Related: Batteries are a looming certification challenge for electric aviation hopefuls
The entire weight of the structure was assumed to be over the cabin, and it collapsed during the test (with effects on the crash test dummies that are “still being determined” but probably weren’t great). NASA cautioned that “there are many other overhead-mass configurations which may behave differently in a crash.” On a positive note, two safety features functioned as intended: an energy-absorbing composite subfloor and stroking seats, which deform during a crash to minimize G-loads on the occupants.
As with any new form of technology, there’s a lot of focus on what can go wrong with eVTOLs, and deservedly so. However, it can be easy to overlook how much can and does go wrong with conventional small planes and helicopters, and how many preventable deaths and injuries over the years have been caused by various cost-driven decisions by manufacturers to not upgrade their designs to the latest standards. When it comes to crash safety at least, it is eVTOLs’ very newness that will force them to be better than what came before.
Write to Elan Head at elan@theaircurrent.com
Subscribe to Continue Reading
Our award-winning aerospace reporting combines the highest standards of journalism with the level of technical detail and rigor expected by a sophisticated industry audience.
- Exclusive reporting and analysis on the strategy and technology of flying
- Full access to our archive of industry intelligence
- We respect your time; everything we publish earns your attention